Understanding The Graduate Management Admission Test geometry section is very important and we are going to give you a gmat geometry cheat sheet on how to master the Graduate Management Admission Test geometry section. this section is very important for those who want to Aspire a masters of Business Administration and other business graduate programs. as far as The Graduate Management Admission Test quantitative section is concerned geometry is a very key part that is challenging but rewarding if you use our gmat geometry cheat sheet properly. in this article we’re going to give you some hints and tips on how you can approach The Graduate Management Admission Test geometry and this gmat geometry cheat sheet will help you too pass the section of the examination.
Understanding The Graduate Management Admission Test Geometry Section
The Graduate Management Admission Test quantitative section is made up of two types of questions namely problem solving and data sufficiency. That geometry questions will evaluate the candidates ability to apply geometric Concepts and reasoning skills to solve problems. the main geometric topics on The Graduate Management Admission Test angles triangles lines that goes polygons and solid geometry.
The Graduate Management Admission Test Geometry Cheat
To deal with The Graduate Management Admission Test geometric questions well you need a well thought out change it that will help you by breaking down the specific geometry tropics and point out the main Concepts formulas and strategies that I needed to address them. Pay close attention to our gmat geometry cheat sheet.
Lines And Angles
The types of lines that are focused on horizontal vertical parallel and perpendicular angles properties
The complementary angles amount to 90° while supplementary angles amount to 180° vertical angles are congruent.
Triangles
There are types of triangles which include equilateral way all sides and angles are equal isosceles two sides are equal scalene no sides are equal. try and go some property the sum of angles in a triangle is 180°,
Pythagorean theorem
any right angle triangle is a squared plus b squared = c squared where c is the hypotenuse As far as sick was a consent the basic Circle properties are radius diameter and circumference as well as the area. concerning central angles and acts the central angles of the same measure is at the intercepted acts while inscribed angles are half the measure of the names intercepted Arc. you should also focus on quadrilaterals and polygons mainly the properties of a square where these features diagnosed by each other it’s right and goes in all sides and angles are equal. that way as far as the rectangle is concerned the opposite side of a rectangle are equal and diagnose are also equal. you should also focus on the interior angles of a polygon and on solid geometry you should focus on volume and surface area formulas of cube cylinders corn spheres which have specific formula for following service area you should also focus on pyramids and premiums comprehending a base area as well as high relationships for different shapes. This is one of the best aspects of our gmat geometry cheat sheet.
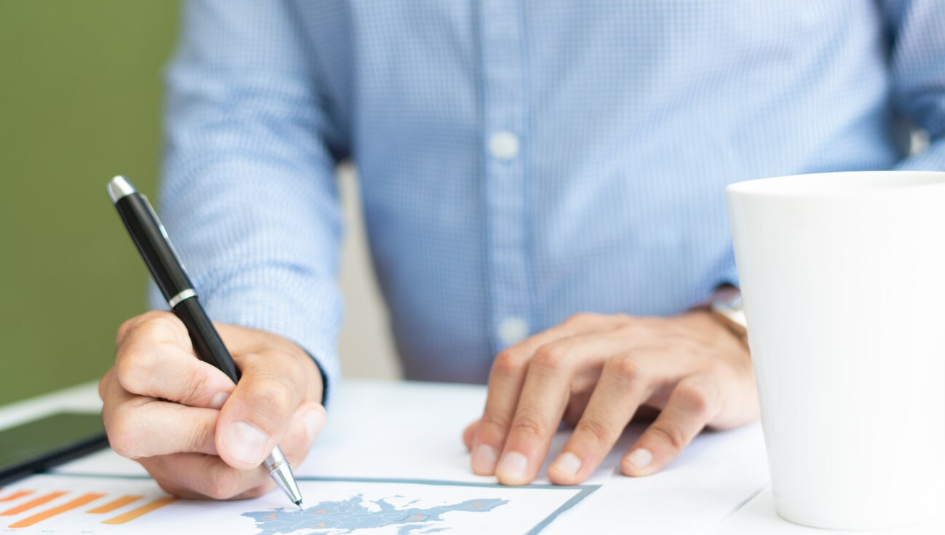
To be able to implement this gmat geometry cheat sheets very well you should be able to practice regularly because practice makes perfect you should be able to apply the concepts that are written in the gmat geometry cheat sheet on more examination so that you apply this skills and make sure that you’ve grasped them. you should be able to know the formulas that have been mentioned in this gmat geometry cheat sheet so that in the exam you can apply them quickly and solve the problems you should also be able to familiarize yourself with the examination structure so that you do not waste my time as far as time is concerned you should allocate your time wisely during the examination making sure that you are giving each question enough time. you can use strategies which make sure that you are focusing less time on the questions that are easy for you and give you much time to the questions that you find more difficult.
To pass the Graduate Management Admission Test geometry is very important to be successful in the quantitative section of the Graduate Management Admission Test.
you should make use of a good sheet like this one which will help you to handle the treatment problems wisely and scoring good marks keep in mind that the gmat geometry cheat sheet comes to help you prepare and practice well by grasping the key formulas and Concepts you can implement the strategies advised in the sheet well wish you luck on you Graduate Management Admission Test and hope this gmat geometry cheat sheet comes in handy for you
In case you think it is too much work for you to take the exam on your own, you can pay someone to take the GMAT exam for you. Our company provides you with the utlimate gmat geometry cheat sheet and other exam cheat sheets to make life easier for you. But , we can make it even way easier by providing test takers who can take the exam in your place. You can contact our customer support for more information and tell them i want someone to take the Graduate Management Admission Test for me and they will be happy to help.